Even the smallest hut can sometimes be the beginning of something big. What started out as a mere market research exercise to identify the demand for construction site huts, has now evolved into the largest modular building manufacturing and assembly operation in the Baltics. This is how the success story of Harmet begins – from some businessmen meeting each other for the first time, finding common ground to develop a new product and persevering through the thick and thin to become one of the leading modular building companies in Scandinavia.
Toomas Kalev, Harmet’s chairman of the board remembers those early days vividly. “We were toying around with the idea of abandoning our metal container business due to increasing cost pressure from the east and were eager to identify market opportunities for manufacturing site huts when our paths crossed with Ivar Valdmaa and Toomas Linamäe from CRAMO, who seemed genuinely intrigued by our plans. We completed our first modular hut within 6-12 months from our initial meeting and were hungry for more, even though at first we had 1-2 people working on the project and our output was limited to 1 hut per month. Today we employ over 800 people and are selling modular buildings to Scandinavia, to the United Kingdom and even the United States,” Kalev gleams with pride. As a firm believer in a hands-on approach, he is no stranger to modular assembly himself. “I always tell our new recruits in the office to go down to the factory floor and get involved – this way you learn at least 5 times quicker than sitting behind the computer all day.”
DESIGN AND ENGINEERING ARE KEY
There have been quite a few learning curves for Harmet during its 20 years of operations, the 2008 financial crisis serving particularly valuable lessons for survival. The numbers were looking great, lulling the enterprise into believing that everything was going well. “But you can never relax when running a business, you must always be on the lookout for improvement and efficiency gains, otherwise you run the risk of losing focus and becoming too laid-back,” explains Kalev. During those tumultuous times Harmet even resorted to knocking up pallets, just to keep the workflow going and the staff busy. “You can’t run away from hard times, but you can learn to deal with them, which is why we are committed to always building reserves and remaining accountable for our actions and promises. We are still using the same brand name, we still have the same people at the top and still answer the same phone numbers – this resilience builds up trustworthiness in the eyes of our partners and our employees alike,” believes Kalev.
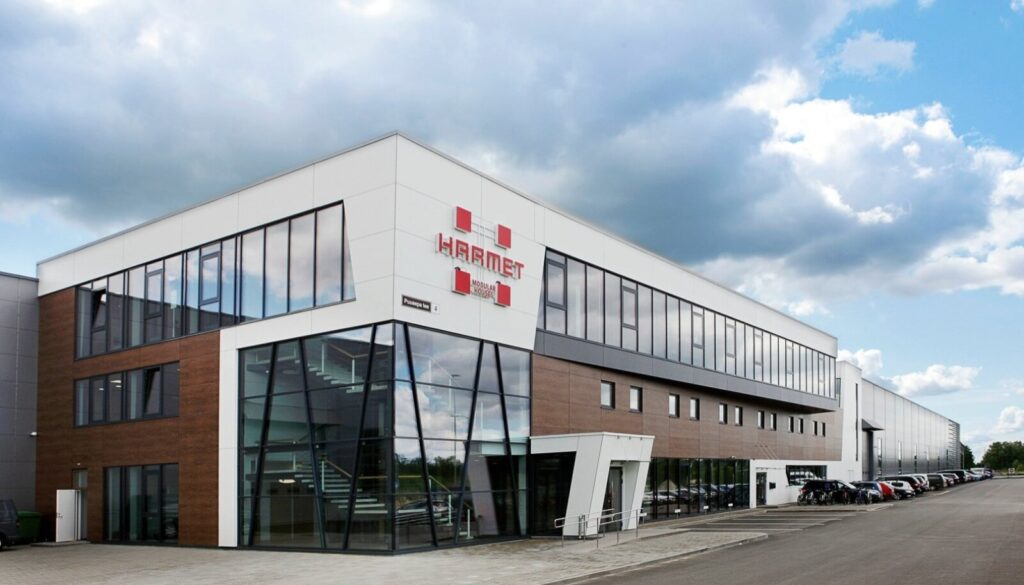
Today Harmet’s greatest challenge is increasing efficiency, as labour costs are on the rise and customers in Scandinavia and further are reluctant to absorb the cost of transportation themselves, leaving Harmet to find the solutions to keep pricing competitive on export markets. A stroke of luck brought Harmet the opportunity to buy pre-owned but little used assembly lines from a modular building factory in St Petersburg some years ago, creating a comfortable buffer for reserve production capacity. But production capacity alone is only a part of the equation – efficiency is achieved through the seamless operation of the entire value chain, from the initial drawings to final assembly and quality control. “Design and engineering is the key to achieving a smoothly running operation, which is why Harmet has established a separate subsidiary for all design and engineering tasks, this will likely grow to become our main business in the future. As they say in our trade – it’s not the builders who create zero-energy buildings, it’s the engineers!” says Kalev.
LENDING A HAND TO THE UK AND THE US
Harmet’s product portfolio primarily consists of residential apartment buildings, hotels, retirement homes, student dormitories, office blocks, schools and kindergartens – essentially any edifice that can be built from pre-fabricated modules. But recently Harmet has expanded to other areas as well, including tailor-made bathroom pods built at the company’s factories in Estonia and in Finland. Another new business venture is a real estate development project in Finland, where Harmet has teamed up with Finnish TILA Group to develop a residential area on 74 hectares of land near Helsinki. “This strongly supports our ambition to evolve from a pre-fab modular building manufacturer to become main contractors ourselves,” stresses Kalev. Expansion to overseas markets comes naturally to Harmet, as 90% of the company’s production output is exported to Scandinavia, predominantly to Sweden, followed by Norway and Finland. Harmet’s sights are set even higher – next in line will be the UK and the US. Skanska and IKEA’s joint venture BoKlok has commissioned Harmet to manufacture several residential apartment buildings to ease the UK’s increasing housing shortage, with the first four apartment buildings expected to be assembled in Bristol during 2021. The pioneering concept will be the first modular apartment building system built on wooden frame to be certified by the National House Building Council. Another new prototype concept is in development specifically for the US housing market, to be manufactured in Estonia and shipped across the Atlantic. Kalev states that using wood as a construction material used to be a Scandinavian characteristic, but during recent years there has been a visible boom globally, with demand for modular buildings made with wooden elements soaring around the world, leading to inquiries from as far away as the United Arab Emirates and even Nigeria. On-site labour costs are increasing rapidly and developers are keen to spend less on the construction site and order pre-fabricated modules straight from the factory. New technological breakthroughs are also paving the way for this, as is evident in the increasing use of cross-laminated timber used for supporting higher and higher structures.
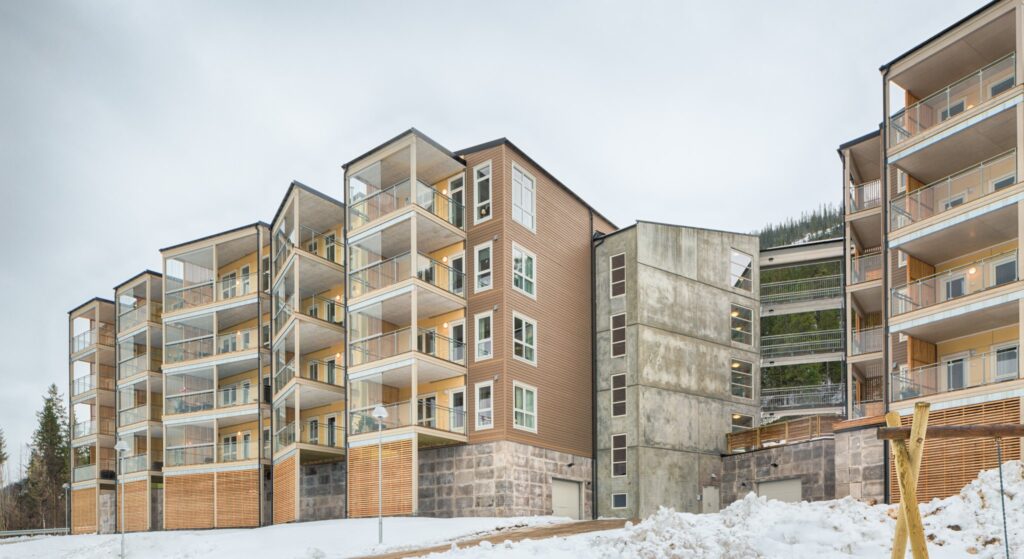
FOLLOWING A VISION OF SUSTAINABILITY
With its 5 factories and 800 employees, Harmet has secured a major competitive advantage over other similar enterprises in the region – the ability to deliver large-scale turnkey projects. “We are capable of handling 20 mEUR building projects and I dare say that there aren’t many others in our region who possess such strengths. Engineering and design forms a crucial part in this, as the economies of scale begin to play a very large role in major projects. Our customers don’t need to know the specifics of modular house construction, our specialists know exactly what solutions to offer. This is particularly relevant now as construction companies have been replaced by real estate funds as the main contractors,” explains Kalev. Using timber as a primary construction material carries a deeper ecological meaning too. Not only does timber act as a carbon bank and contribute to battling the effects of climate change and global CO2 levels, but it also provides a healthier environment for the day-to-day users of the buildings. “We follow a vision of sustainability, which is why we use solar energy at our factories and every year plant as many new trees as have been used in our products during the previous year. Just like we aim to avoid making mistakes when designing, manufacturing or assembling our modular buildings, we want to ensure that we don’t harm the environment either,” concludes Kalev.
Source: Tradewithestonia.com