The history of Estonian timber house builder Timbeco goes back several decades to a modest family operation at the dawn of capitalism in the early 90s, building wooden log houses under the name Palktare for affluent Scandinavian and German buyers. 2006 became a turning point in the company’s development, as demand for wooden buildings went into decline in Scandinavian markets, due to more stringent energy-efficiency requirements.
However, the markets needed affordable yet elegant pre-cut buildings that could be assembled on-site using post-and-beam construction methods. The first element buildings were assembled in 2007 and soon Timbeco moved on to hybrid constructions – wooden facades and roofing for steel-and-concrete buildings, a business area in which there was little competition in Estonia.
Wooden masterpieces
Hybrid constructions remained one of the company’s main products until 2018 and featured several unique masterpieces that are a source of pride for Timbeco to this day. Among these are the fantastic Oodi public library building in Helsinki, Finland and the prefab timber wall elements for an 18-storey apartment building in Stavanger, Norway. The range of Timbeco’s product portfolio is certainly impressive, from privately owned log houses in Japan to hospitals and industrial buildings worldwide.
Today the focus at Timbeco is on building modular houses, engineered by its subsidiary Timbeco Woodhouse. Some may find the distinction between element houses and modular houses confusing, but Timbeco’s sales manager Tõnis Vaiksaar has a simple explanation for the conundrum. “Element houses are constructed from prefabricated timber frame elements and assembled on-site, while modular houses are built at the factory, can be erected in just hours, and are movable.”
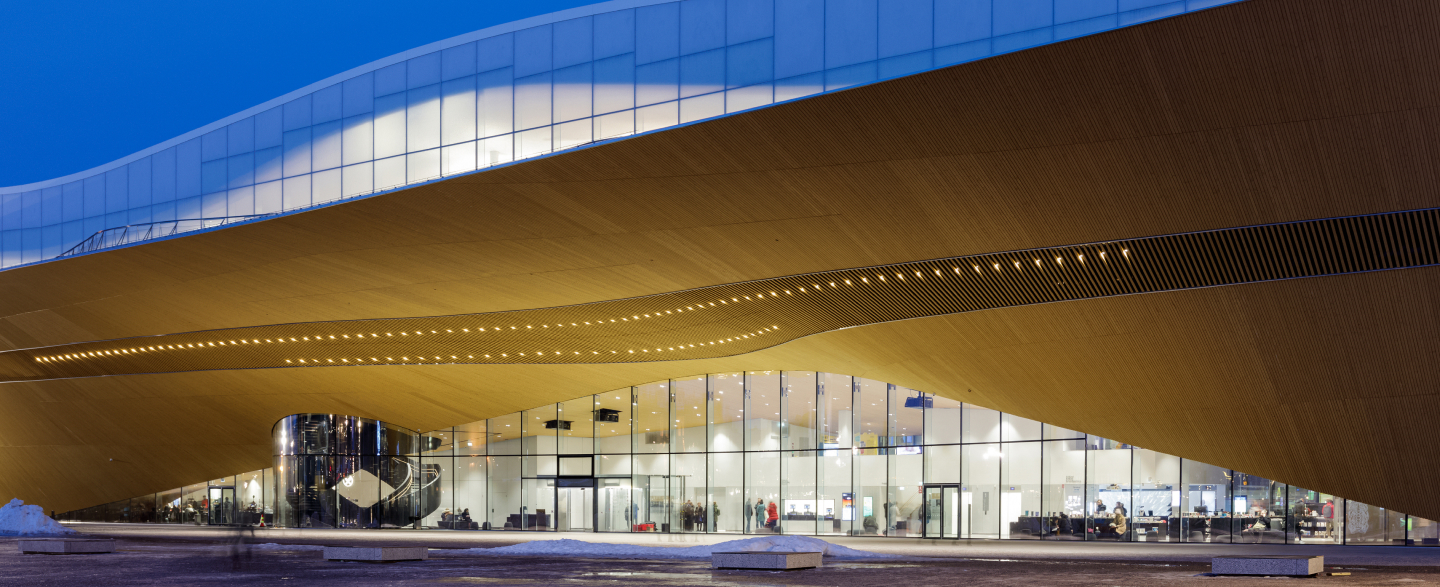
Photo: Sergei Zjuganov
The cult of timber
Timbeco’s founders and managers describe themselves as members of a cult, whose objective is to make use of as much timber as possible. “Timber is recyclable and renewable and we see the entire construction sector moving in this direction, with more and more wooden cities emerging. Thankfully, this has been noted by local governments and national policymakers as well, giving us extra oomph to push ahead,” says Vaiksaar.
Global demand for more sustainable materials has extended Timbeco’s export range to all over Europe, with Scandinavia, Central Europe, Switzerland, Holland and Germany leading the list of key markets. But now the company’s sights are set on a new market niche – building plug-and-play self-service stations. “The possibilities are endless here and we can’t even imagine how our products might eventually be used by our clients; it could be anything from self-service petrol stations to mini-kiosks and even airBnB accommodation units,” Vaiksaar believes. The important aspect here is that, depending on local rules and regulations, it may be possible to set up 100-square-metre modular houses without building permits.
Project managers with manufacturing capabilities
The industrial manufacture of buildings is a very complex process, entailing a great deal of coordination and planning, not to mention communicating with all the parties involved. What sets Timbeco apart from the rest is the company’s ability to act as a project manager and not just a manufacturer. “It’s a chicken-and-egg question – whether we are project managers with manufacturing capabilities or manufacturers with project management capabilities,” comments Vaiksaar with a smile. “Both are equally important and form the solid foundation for our international success.” The majority of Timbeco’s team hold an engineering degree from Tallinn University of Technology and the company can rely on its in-house knowledge for almost any practical problem that needs solving.
Developing engineering solutions, producing massive wood elements and organising on-site construction of the Oodi Helsinki Central Library has been the most challenging project for Timbeco to date. “Our mission wasn’t to supply the wooden roofing elements, but to sell our project management skills. In other words, we provide a package service that results in a product and not the other way round,” says Vaiksaar. Oodi’s success has substantially increased the number of enquiries from Finland and elsewhere in Scandinavia.
Although Timbeco’s people are self-confessed members of the wood cult, they are not opposed to using concrete or other materials in construction. But they prefer wood and composites where it can be combined with other materials. “We should stay away from extremes – timber may not be the ideal material for all spaces and purposes. However, it remains unmatched by others for sustainability. If we followed spreadsheet logic in everything we do, all houses should be built of metre-thick timber materials. But that wouldn’t make sense,” reasons Vaiksaar. It’s up to the engineers to determine the best qualities of different materials and combine them into a complete bundle in the most responsible and efficient manner.
“We should stay away from extremes – timber may not be the ideal material for all spaces and purposes. However, it remains unmatched by others for sustainability.”
Estonians are experts
The wooden house industry in Estonia is punching far above its weight, as this small country exports more wooden houses than any other in the world. There are larger manufacturers than Timbeco elsewhere, states Vaiksaar, but they tend to focus on domestic markets. “Nobody knows more about regulations in different markets than Estonians, as our CE certificates prove.”
The reason for Estonia’s success in this market segment lies in its people. “Estonians are smart and reliable. We no longer focus that much on the manufacturing aspect, but rather on design, project management and installation,” observes Vaiksaar. Estonian manufacturers have moved far beyond the low-cost segment of the market to the high-quality niche and are now able to focus more on engineering and technical consultancy. This transformation can also be seen in the changing customer profile. Today’s clients tend to be developers who run small, efficient teams and outsource 90% of services, only handling local market know-how and smaller competences on their own.
In Timbeco’s dreams, busy and noisy construction sites are a distant memory. “Our subsidiary, Timbeco Modular Systems, constructs apartments, duplexes, villas and larger buildings, covering all aspects from manufacturing to final installation. We believe that the construction site of the future will be in the form of an assembly site, where work gets done quickly using the fewest people absolutely necessary. Developers are keen to get their houses with minimal waiting time, much like ordering a food delivery from a restaurant.”
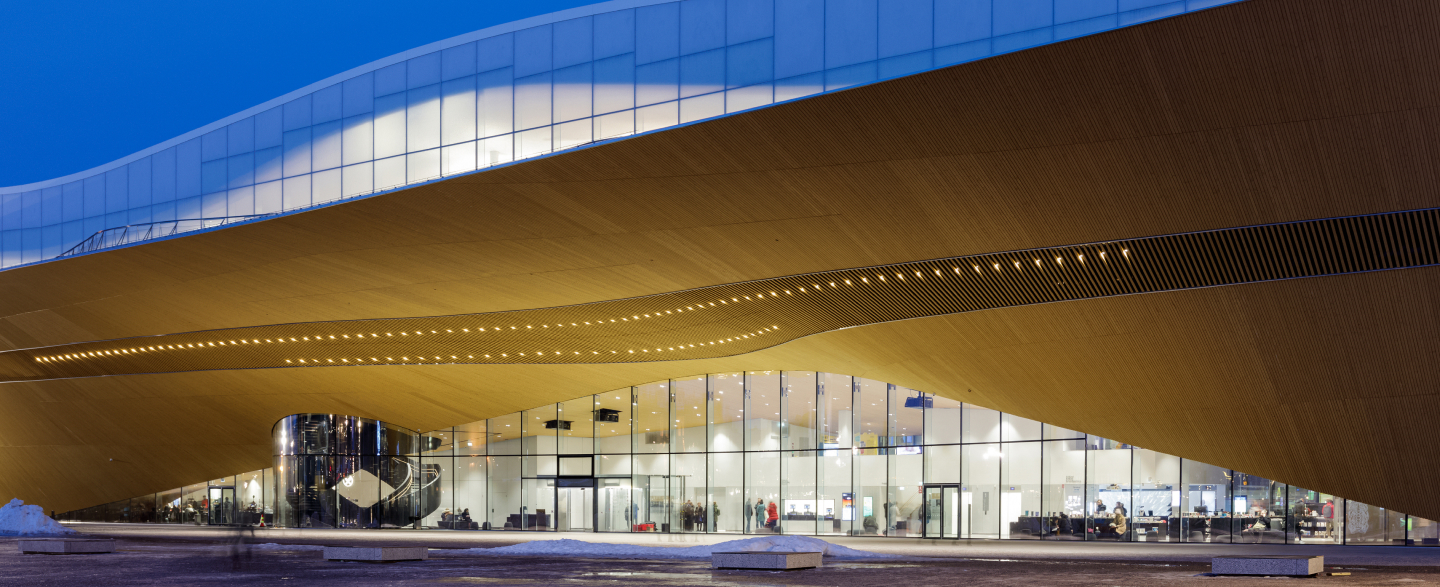
Photo: Sergei Zjuganov